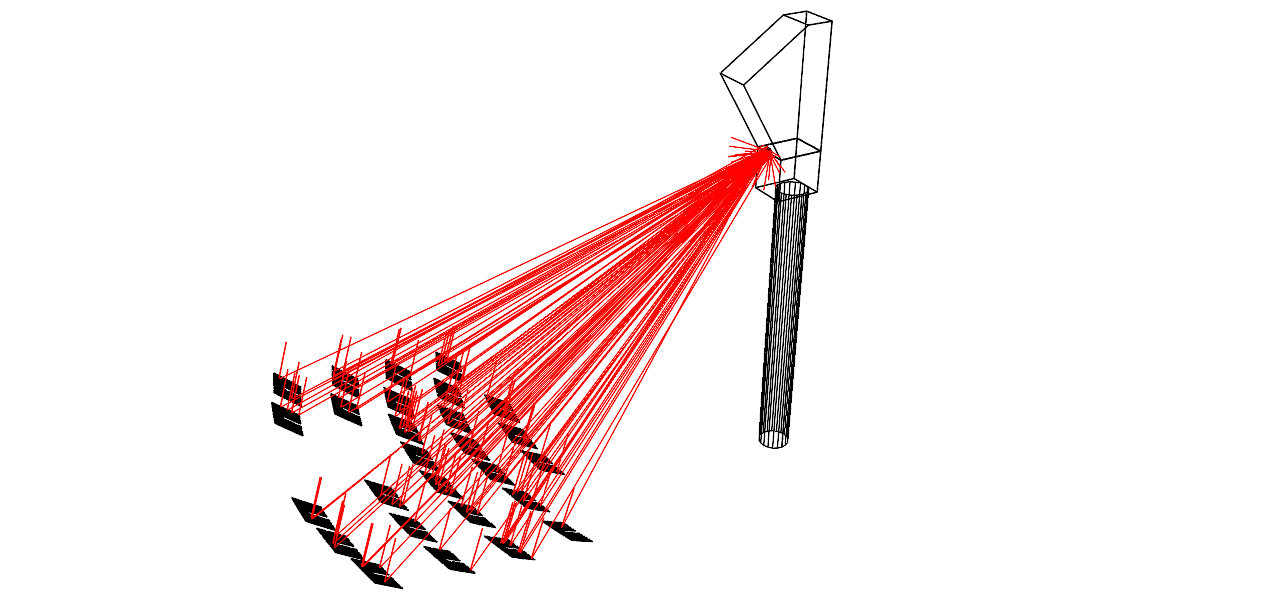
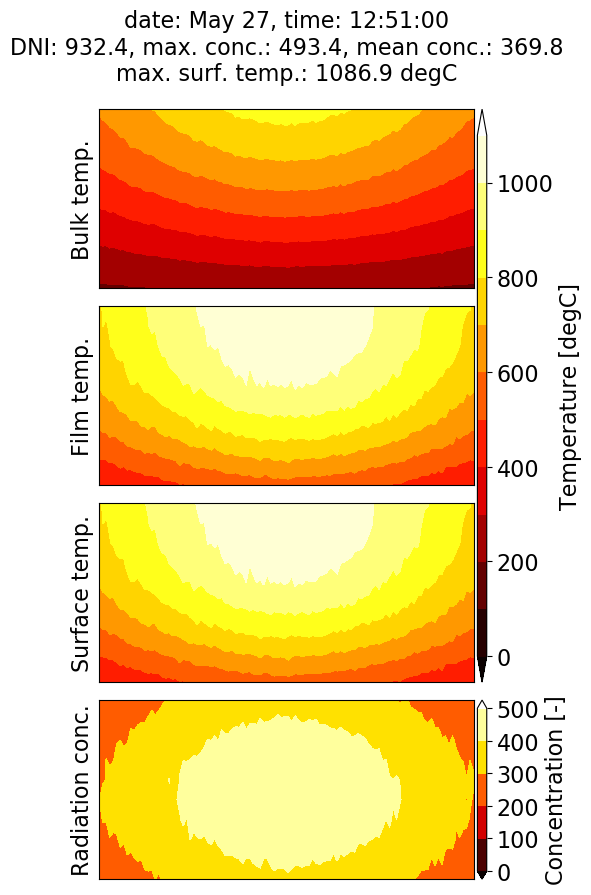
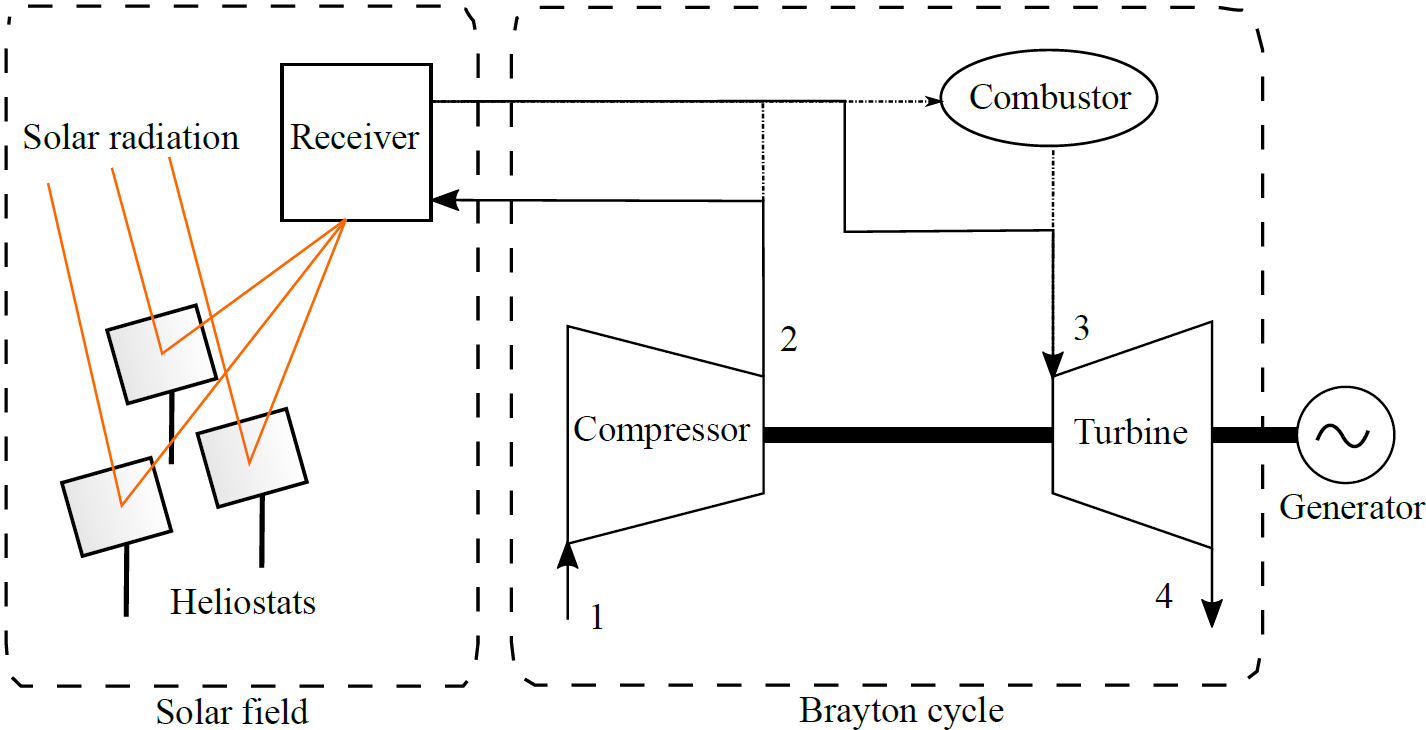
For the preliminary design of the entire plant and its individual components, the scope of functions and the modes of operation were elaborated and defined and, in parallel, corresponding heat and mass balances were created on a static basis using a commercial planning tool. In cooperation with the project partners, the associated process flow chart was developed.
For performance predictions of the POLYPHEM system based on annual yield assessment, but also for short-term forecasting for the optimization of prototype operation, appropriate dynamic simulation models for the various plant components and for the entire system are necessary. They should be highly accurate and with a sufficient level of detail, but also computationally fast enough to be used for annual simulations – a Digital Twin of the real plant.
At Fraunhofer ISE, this simulation tool chain has been created based on our powerful in-house software tools – Raytrace3D for the optical assessment of the Solar Island (heliostat field and receiver) through ray tracing and ColSim CSP for thermo-hydraulic system simulations of the POLYPHEM cycle, including receiver, gas turbine, ORC power block and thermocline storage.
Over the duration of the project,
- a simulation model for the entire plant has been developed,
- very detailed models have been developed for some key components of the POLYPHEM system: air receiver and gas turbine
- a control approach covering different operation modes has been integrated
- a techno-economic optimization of the system with different cost scenarios has been performed
Particularly, the optical assessment based on Raytrace3D directly led to relevant insights that affected the prototype design process.
The compressor and micro gas turbine (topping cycle) are two key elements of the combined cycle as the exhaust gas from the turbine satisfies the heat requirement of the storage and the ORC power block (bottoming cycle) and thus need to be modeled properly for an accurate performance prediction. Detailed dynamic models for the compressor and the micro gas turbine have been created based on performance characteristic curves. The curves are generated through an adapted methodology prior to system simulation.
Further Information on Project »POLYPHEM« and its Tasks:
Research Project: Polyphem – Small-Scale Solar Thermal Combined Cycle (Gas Turbine/ORC)
Task: Development of a camera-based measurement system for circumsolar radiation
Task: Simulation model for the POLYPHEM prototype – Digital Twin