News #19
Circular Water Strategies in Solar Cell Manufacturing Could Realize Potential Water Savings of up to 79 Percent
Researchers from the Technical University of Berlin, Rena Technologies GmbH, and the Fraunhofer Institutes for Building Physics IBP and for Solar Energy Systems ISE have for the first time created a comprehensive model of the water flows in a solar cell factory with a production capacity of 5 gigawatts (5GWp) per year. Using this model as basis, they tested the introduction of two different strategies for circular water use. The results show that a reduction of up to 79 percent in the water consumption and up to 84 percent in the wastewater is already technically possible with today's production technologies. This would mean that the construction of new solar cell factories in locations with less water availability are also feasible. The study is freely accessible in the latest issue of Solar Energy.
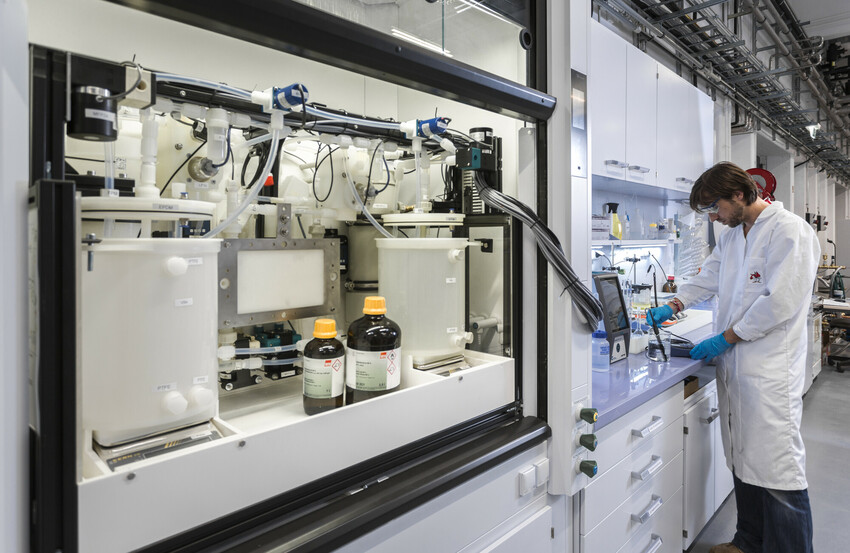
The research team analyzed the water consumption, wastewater, and material flows for a PERC solar cell production factory with an annual production of 5GWp. The results are also interesting for factories in which heterojunction or TOPCon solar cells are manufactured or for factories which are to be converted for this purpose, as the wastewater streams for these cell types are very similar.
"Based on the model for the PERC production plant, we analyzed different options for saving and recycling water," explained Peter Brailovsky, one of the two main authors of the study and a researcher at Fraunhofer ISE. "We can recommend two approaches: The reuse of low contaminated wastewater (LCR) and the so-called "Minimal Liquid Discharge" (MLD) approach, in which certain residual materials are recycled and used elsewhere." For example, etching solutions left over from solar cell production can be used in the cement production.
"The results of the MLD scenario show that savings of up to 80 percent in the freshwater demand and in the wastewater can be achieved in the solar cell production factory modeled," said Jascha Reich, second lead author of the study and researcher at the Technical University of Berlin. "With the LCR approach, savings of up to 40 percent can be achieved." At the same time, implementing the savings measures would not impose any additional costs on production. On the contrary, it would in fact mean a slight savings in costs overall. In addition, a circular water strategy greatly reduces the risk of a factory shutdown due to water shortages, which can amount to weekly costs of around 1.9 million euros, for example, during heat waves in summer.
Solar cells are a very sustainable product in themselves. When integrated into a photovoltaic module, the energy required to produce them is amortized within a very short time - typically within 1.3 years for photovoltaic systems in Central Europe. "This, however, should not make us complacent," said Dr. Jochen Rentsch, department head of Technology Transfer in the Division of Photovoltaics at Fraunhofer ISE. "As every production factory in the manufacturing industry, photovoltaics should also become part of a circular economy."
Downloads and Links
Last modified: