Press Release #24
Solar Cell Contacts From Tubes – Innovative Fine Line Metallization Technology Promises Higher Efficiency Values
Together with industrial partners MERCK, HERAEUS and ASYS, researchers from the Fraunhofer Institute for Solar Energy Systems ISE have developed innovative new materials and contactless techniques for applying ultrafine, homogeneous contact fingers to solar cells. This ‘dispensing’ technology can be easily integrated into conventional silicon solar cell production lines where it replaces screen printing as the method of applying front side metallization: Consequently material usage is reduced, contact fingers are thinner and more of the semiconductor surface area is exposed to sunlight, which results in increased current collection and relative improvements in efficiency of around two percent. The new technology can also be used to optimize further production steps in solar cell manufacture.
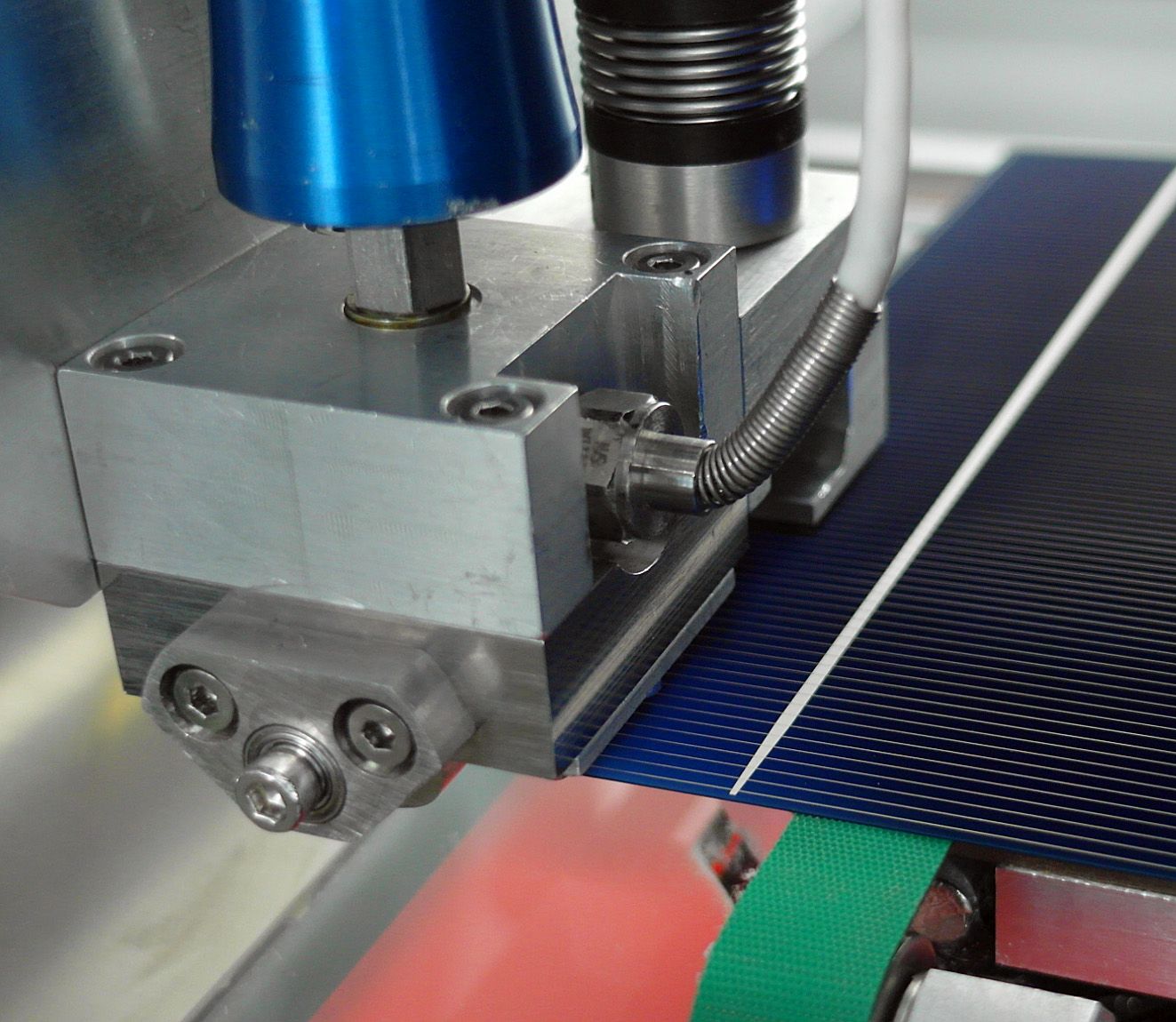
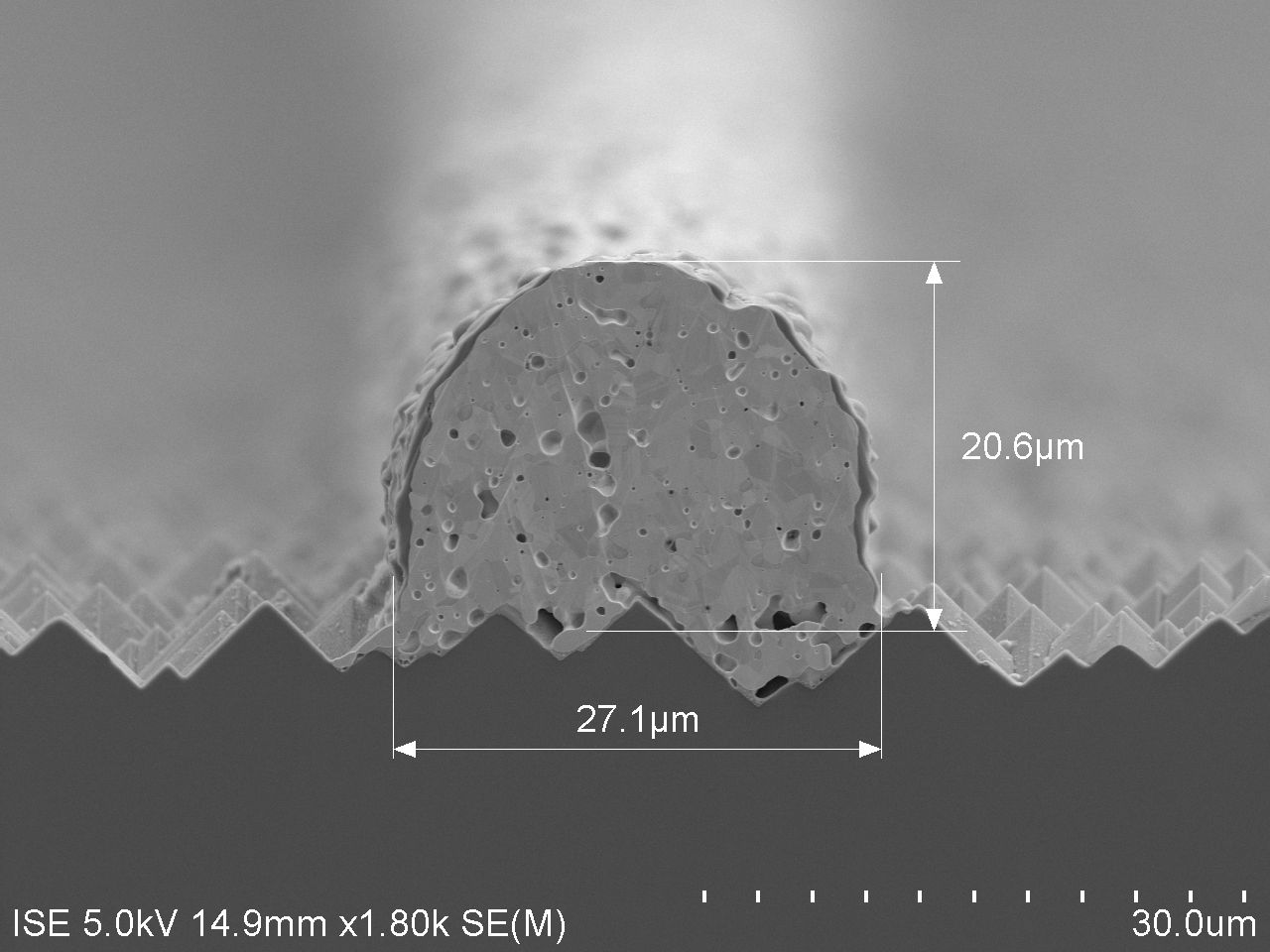
Using the dispensing technology, new materials developed by MERCK and HERAEUS are placed on the surface of solar cells in a contactless printing process which utilizes ultra-fine openings in a strictly parallel printing head. In this new method, also called extrusion, materials are pushed through the extremely small openings of a printhead in a manner similar to toothpaste being pushed through the end of a tube, only that the researchers here use nozzle diameters the thickness of a human hair (approx. 50 µm) and that many nozzles work in parallel to quickly produce the desired structures. “The Photovoltaic Technology Evaluation Center PV-TEC at Fraunhofer ISE provides us with a truly excellent infrastructure for these types of new development,” says project manager Dr. Florian Clement. “We are able to carry out every single step here, from detailed characterization of media flow behavior to the manufacture of highly efficient silicon solar cells. We also simulated the fluid dynamics of the extrusion process here to develop the printhead architecture.” This allowed the dispensing heads to be optimized in a series of iterative steps and then tested for practical feasibility in the application lab.
By drawing together all the different experiences gained, the industrial partner ASYS developed an automatic dispenser that started operation at Fraunhofer ISE in spring 2014. The newly developed dispensing heads can be integrated into and controlled by this highly flexible machine, which itself can be easily incorporated into conventional solar cell manufacturing processes in order to apply the desired metallization structures onto cells with maximum precision.
Several hundred solar cells have already been processed using the equipment together with a special printhead optimized for front side metallization. Fine line contacts with widths under 35 µm have been achieved here on industrially preprocessed solar cells. Compared to industrially widespread screen printing processes, this technique reduces the contact width by around a third while maintaining the same cross-sectional contact area – all in all impressive confirmation of the technology’s performance. The new procedure also enables extremely homogeneous extrusion of the contacts, meaning that the ‘mesh marks’ often seen in screen printing processes do not occur here.
Fraunhofer ISE’s dispensing technology has the potential to replace conventional printing machinery in solar cell manufacturing, since only slightly modified pastes are used, print speeds can be increased, and even the firing process remains the same. Furthermore, it offers additional room for savings in dual print processes where busbars and contact fingers are applied to solar cells in two separate printing steps so as to achieve even higher efficiencies with reduced silver consumption. Compared to screen printing, the contactless print process here avoids the need for an additional drying stage after busbar printing – printing is wet on wet and one dryer less is required. The contact-free process also promises to improve reject rates when thinner silicon wafers are used.
Solar cell manufacturers are already showing great interest in the dispensing technology and are providing test wafers to be metallized at Fraunhofer ISE using the new system. Plans for the next phase include developing even higher performance printheads and integrating them into the system.
The work, under the project name ‘Gecko’, is being jointly funded by a grant from the Federal Ministry for Economic Affairs and Energy (BMWi) and through finance from the industrial partners listed. Findings are to be presented at the “Fifth Workshop on Metallization of Crystalline Silicon Solar Cells” on October 20-21, 2014 in Constance, Germany.
Last modified: