Press Release #16
Cables No Longer Needed – High Efficiency Inductive Charger Developed for Electric Vehicles
At the Fraunhofer Institute for Solar Energy Systems ISE in Freiburg, scientists developed a highly efficient system to inductively charge electric vehicles. The wireless energy transfer to the car battery is carried out by means of an electromagnetic field between two coils: one installed in the car and a second, stationary coil integrated into the street or the parking place. A cable connecting the charging station and the electric vehicle is no longer necessary with this system. The first prototypes of the wireless charging system prove to be very efficient: An efficiency of 97.4 percent was achieved for the inductive power transmission at a coil distance of 13 cm. The transmitted power reaches up to 22 kW.
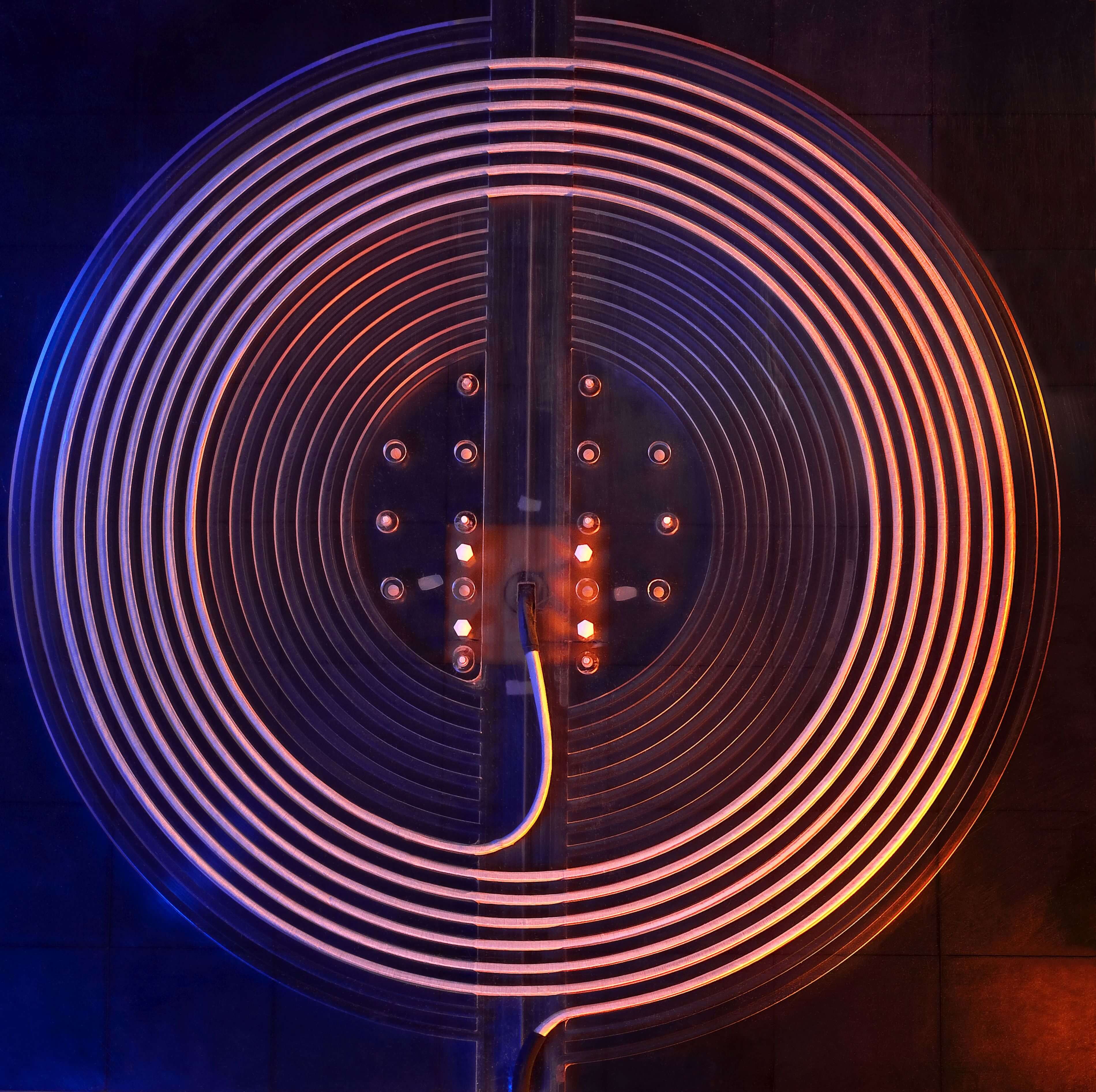
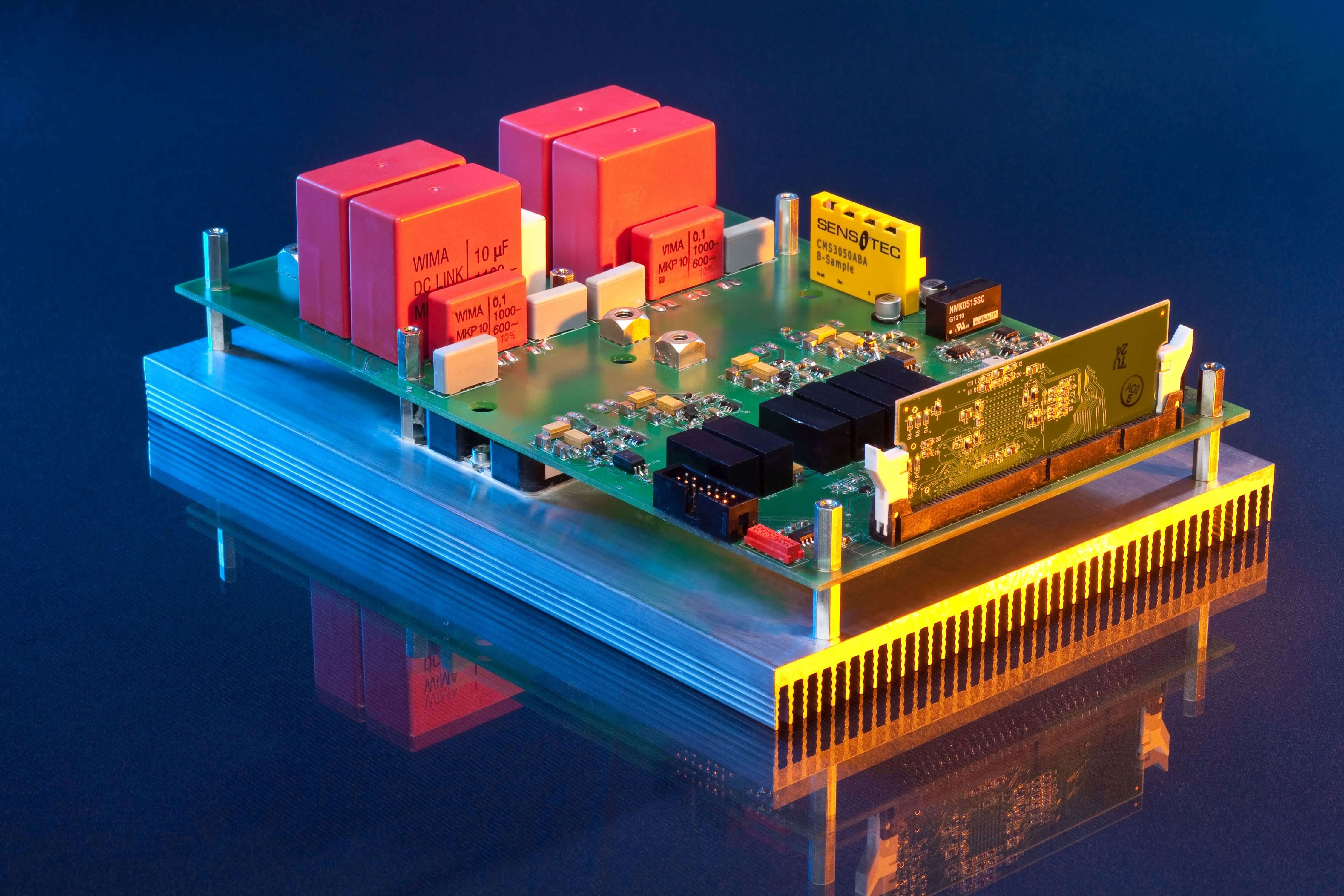
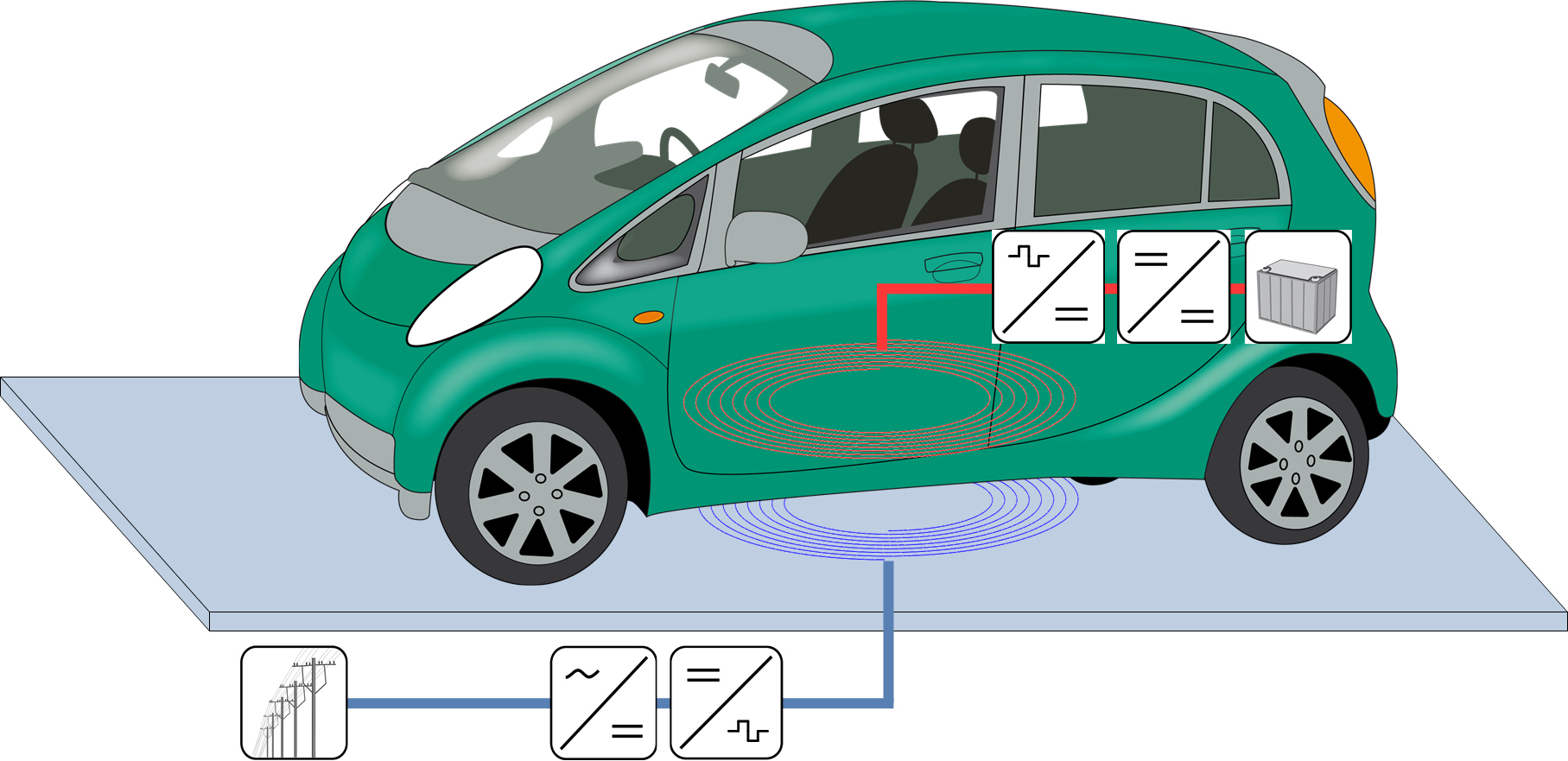
All of the necessary power electronics for wireless energy transfer, the coil system and the control technology were developed and constructed at Fraunhofer ISE within the framework of the Fraunhofer project “Shared use of e-mobility: vehicles, data and infrastructure“, or GeMo for short in German. Among other things, the scientists in Freiburg have developed a resonant power converter. With a resonance circuit and a stationary coil, this device creates a high frequency magnetic field which transfers the power to the mobile coil located in the electric vehicle. Another converter reshapes the high frequency current of the coil into direct current for charging the battery. The focus was to optimize all sequences in the inductive charging process chain.
By employing new semiconductor devices made from silicon carbide (SiC), the efficiency of the various power converters used in the charging system could be increased greatly. Due to the low switching losses, SiC transistors allow high switching frequencies of 100 kHz which makes the mechanical construction very compact and much lighter compared to conventional devices. Other losses could be minimized by optimizing the coil and the resonant circuit. With special capacitors on the stationary and the mobile side, the reactive power requirement and scatter field of the coil were compensated. Also, there shall be no reactive power exchange between the power electronics and the coil.
To make the charging system complete, the researchers worked both on a bidirectional inverter for connecting the stationary part of the system to the grid and on a bidirectional converter for connecting the mobile part of the system to the battery. These allow continuous, bidirectional operation of the charging system, which can not only take power from the grid and feed it into the battery but also feed the power stored in car battery back into the grid. For the complete system, the researchers give an efficiency of up to 95 percent and a maximum transmitted power of 22 kW. With this system, it is possible to charge a conventional electrical vehicle battery to 80 percent of its nominal capacity in less than one hour. “Wireless charging of electric vehicles increases not only the comfort for the user, but also enables an efficient vehicle/grid interface without involving the user,” says Stefan Reichert, Team Leader of Grid Integration and Electric Mobility at Fraunhofer ISE.
About the Fraunhofer Project “GeMo”:
In the Fraunhofer project called “Shared use of e-mobility: vehicles, data and infrastructure”, or GeMo for short in German, six Fraunhofer institutes are researching energy interfaces and information technology interfaces between the users, vehicles and infrastructures. The work is supported through the Fraunhofer research program “Beyond Tomorrow Project”.
http://www.gemo.fraunhofer.de/
Last modified: