Presse Release #10
Fraunhofer ISE Team receives Innovation Award Laser Technology 2014 – European photovoltaic research recognized for its innovative strength
A research team at Fraunhofer ISE was awarded the Innovation Award Laser Technology 2014 for its Laser Fired Contact (LFC) technology used for the production of highly efficient silicon solar cells. Dr. Ralf Preu, division director of Production Technology and Quality Assurance, Dr. Jan Nekarda and Martin Graf, all scientists at Fraunhofer ISE, accepted the award on May 7, 2014 at the festive Coronation Hall of Aachen’s city hall in Aachen, Germany. The European science award is bestowed every two years by the associations Arbeitskreis Lasertechnik e.V. (AKL) and the European Laser Institute (ELI). An international jury comprised of nine experts chose three finalists out of a total of 23 applicants.
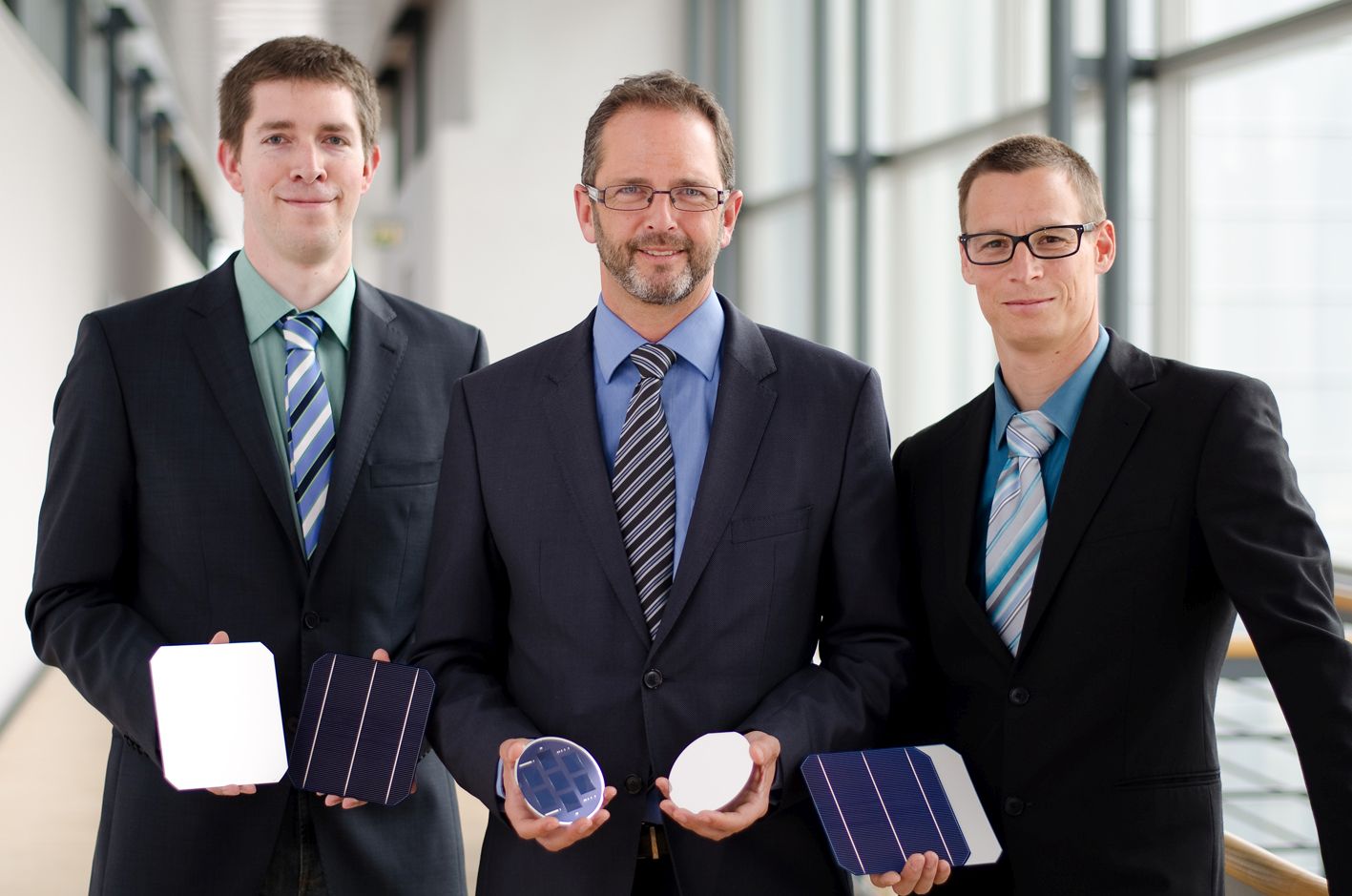
“We are delighted to have received this honor that is not only a recognition of our work but also the innovative strength of photovoltaic research and industry throughout Europe,” says a pleased Ralf Preu.
The prize-winning LFC technology is a cost-efficient procedure for rear-side contacting and allows current collection to take place on the rear side of silicon solar cells. In less than a second, a pulsed laser drills several ten thousand contacts in an aluminum layer on the rear side of a solar cell. LFC combines high efficiency potential with low manufacturing costs, since it replaces the expensive and slower structurization steps previously necessary for the rear side passivation of solar cells. Fraunhofer ISE’s work on LFC technology began more than ten years ago under the direction of Ralf Preu and has led to patented procedures.
“With the LFC technology of the first generation, we proved that highly efficient solar cells could be manufactured with fast laser processing. With the second generation we moved the manufacturing procedure up to the industrial processing level,” explains Ralf Preu. “Now we are working on the third generation of this technology, in which we expect to take a large innovative step forward towards the cost-effective production of highly efficient solar cells.” The Freiburg researchers first applied the LFC technology to aluminum films grown by vapor deposition on the rear side of solar cells. Ten years ago the Fraunhofer researchers used this process to achieve a world record efficiency for multi- crystalline silicon solar cells, which is still valid today. The necessary adaption of the process for screen printed aluminum – the wide-spread industrially available metallization technology – was successfully carried out. About four years ago, the technology transfer to the industry partner Q-Cells began. Q-Cells continued to optimize the technology and achieved cell and module record efficiencies of 19.5% for large-area multi-crystalline solar cells and 18.5% for standard-sized modules. Compared to standard technology, the excellent performance of the PV modules manufactured with this new technology has been repeatedly confirmed in field tests. The researchers did not stop here. They continued their pursuit for further cost optimizations and higher efficiencies. A new procedure, currently under investigation, is on its way to reaching production maturity. Here, conventional aluminum foil is welded to the silicon wafer by means of laser radiation, adding another significant improvement to the manufacturing process of rear-side passivated silicon solar cells.
On the occasion of the award ceremony, Ralf Preu was conferred the titles of AKL Fellow and ELI Fellow. The Innovation Award Laser Technology, endowed with €10,000 EUR, was handed over by Ulrich Berners, Dipl.-Ing., president of the Arbeitskreis Lasertechnik AKL e.V. and Dr. Paul Hilton, president of the European Laser Institute ELI. The prize is awarded to individuals as well as project teams, whose skill and dedication has led to an excellent innovation in the field of laser technology which has demonstrated a commercial value to the industry. Further information about the award and the finalists can be found at: www.innovation-award-laser.org
Last modified: